1750TEU系列集裝箱船是廣東中遠(yuǎn)海運(yùn)重工首制集裝箱船項(xiàng)目。在該船型的設(shè)計(jì)階段,針對機(jī)艙底層的設(shè)備、管路布置,技術(shù)部聯(lián)合各工區(qū)進(jìn)行了深層次的反復(fù)討論,最終制定了單元內(nèi)場組裝、分段吊裝的施工方案。該方案較大程度保證了機(jī)艙底層在涂裝前的完整性,將機(jī)艙底層的設(shè)備、管路安裝工作,從船臺階段前移到了分段階段,有效減少了總組和船臺階段的動火作業(yè)點(diǎn),減少作業(yè)管理的復(fù)雜性,提高作業(yè)管理安全性,且對機(jī)艙底層的油漆保護(hù)意義重大。
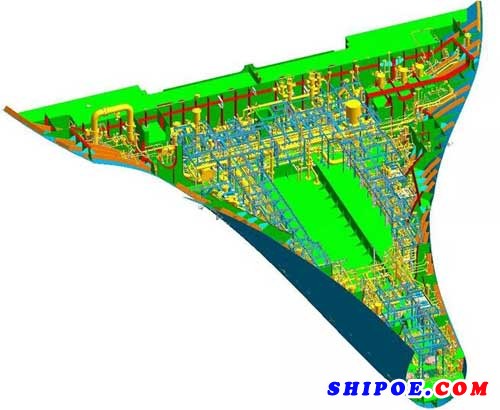
機(jī)艙底層舾裝件安裝工序前移
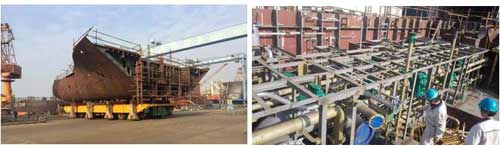
機(jī)艙底層分段舾裝工序前移
經(jīng)過統(tǒng)計(jì),機(jī)艙底層101和102分段在涂裝之前,一共安裝完成了管件1057根(占機(jī)艙預(yù)裝管子總數(shù)的1/4),支架786個,閥附件266個,艙室完整性報(bào)驗(yàn)完成8個,艙室密性報(bào)驗(yàn)完成8個,艙室強(qiáng)度試驗(yàn)1個,電舾件352件,鐵舾件404件。由此,機(jī)艙底層的盆舾裝(機(jī)艙底層主機(jī)周圍的舾裝件安裝,環(huán)境像一個盆一樣,俗稱“盆舾裝”)在進(jìn)棚打砂涂裝前基本全部完成,有效縮短了后道工序的施工時間。
花鋼板和壓載泵提前制作安裝
除此之外,結(jié)合前四條船機(jī)艙底層的施工經(jīng)驗(yàn),分段工區(qū)對機(jī)艙底層單元完整性提出了更高的要求,嘗試在分段涂裝前完成花鋼板和壓載泵進(jìn)行試裝工作。因此,分段工區(qū)聯(lián)合技術(shù)部、項(xiàng)目組、機(jī)電工區(qū)等多個部門進(jìn)行協(xié)商討論,綜合計(jì)算工序前移產(chǎn)生的人工成本和所需的周期,對比節(jié)省的成本和時間,同時考慮工序前移可能存在的返工修改等。經(jīng)過多方研究論證,最終一致認(rèn)為該方案可行,并決定從N804船開始正式實(shí)施。
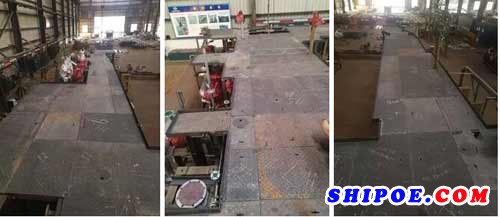
機(jī)艙底層花鋼板在分段階段安裝
N804船機(jī)艙底層單元在內(nèi)場組裝完成以后,基于技術(shù)部的圖紙,對每塊花鋼板的尺寸進(jìn)行現(xiàn)場測量,繪制成花鋼板的下料圖,交由等離子切割機(jī)組進(jìn)行下料。下料完成以后,運(yùn)送回單元平臺進(jìn)行鋪設(shè),四邊鉆孔安裝沉頭螺釘,閥件位置開孔安裝合頁。整體完工以后,交由質(zhì)量管理部和機(jī)電工區(qū)驗(yàn)收,最后對每一塊花鋼板進(jìn)行編號、拆除、涂裝、交由機(jī)電工區(qū)保管,船臺階段具備回裝條件之后,可以根據(jù)編號直接回裝。
經(jīng)過統(tǒng)計(jì),單元在組裝階段,共完成了122塊花鋼板的預(yù)安裝工作,安裝面積達(dá)到48平方米,鉆孔攻絲約500個,安裝沉頭螺釘約500個,閥手柄位置開孔安裝合頁60個,進(jìn)一步提升機(jī)艙底層單元完整性的同時,也在較大程度上減少了后行的施工量,節(jié)省了后行的施工周期。
提高壓載泵進(jìn)口管安裝精度控制消除質(zhì)量隱患
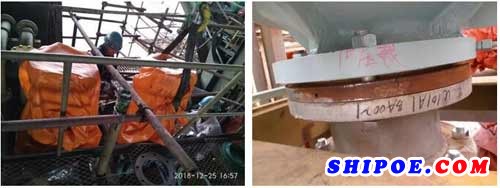
壓載泵進(jìn)口管安裝精度控制
N804船分段階段單元吊裝完成以后,為了避免壓載泵進(jìn)口管因?yàn)榈跹b變形造成管口精度偏差,給后行階段施工帶來質(zhì)量隱患,分段工區(qū)聯(lián)合機(jī)電工區(qū)對7臺壓載泵完成了試裝工作,經(jīng)過兩天的吊裝和管路調(diào)整,7臺壓載泵的進(jìn)口管全部和壓載泵進(jìn)口吻合,消除了船臺階段管口不對中的質(zhì)量隱患,降低了施工難度,減少了施工量,縮短了施工周期。
“學(xué)川崎”的重要目的就是持續(xù)改善,降本增效。廣東中遠(yuǎn)海運(yùn)重工1750TEU集裝箱船機(jī)艙底層單元完整性的進(jìn)一步提升,既節(jié)約了成本,又提升了效率,同時保障了質(zhì)量和安全,是“學(xué)川崎”落實(shí)到生產(chǎn)最直接的體現(xiàn)之一。